The Expertise
Dreampell’s expertise
The entire production process is carried out at Dreampell’s Scandicci-based facilities, where the company’s craftsmanship, expertise and high-performance machinery provide control over all phases of leather processing and the finished product.
Product development, modelling, cutting, preparation, assembly, re-finishing and testing for quality control of the final product with the customer: these are all the stages that the company is able to follow during the production cycle, including every aspect of processing.
The production process that the company has structured over the years is organised down to the smallest detail to allow perfect control over the individual stages of leather processing.
The services offered:
- Product development and pattern making
- Raw material quality control
- Die cutting or automatic cutting
- Preparation
- Assembly and finishing
- Quality control and packaging
- Shipping
Product development
and pattern making
A dedicated pattern-making and product development area has been created within Dreampell’s facilities to provide specific support to customers so they can create, study, prototype and industrialise new products.
A team of dedicated experts develops creative designs through the use of technological processes and new programming tools that enable CAD finished models.
The company also offers the possibility of having models developed traditionally by hand.
From the customer’s sketches and style, Dreampell is able to develop the first prototype, which will be transformed into an actual model after various stages of defect clearance.

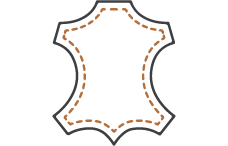

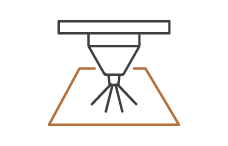
Raw material control, cutting and preparation
Logistically, Dreampell’s factory is designed to receive incoming materials, which are then checked before being sent to the various departments.
After careful inspection, the leather is transferred to the cutting department, which is carried out in-house or by detached companies working permanently for Dreampell.
The cutting is carried out using automatic machines and traditional dies, all of which are meticulously supervised by the head of the department.
After the cutting phase, the leather is sent to the preparation phase, where the raw material is brought to the desired thickness by splitting and fleshing.
Before arriving at the assembly stage, pre-assembly is carried out by means of robotic gluing machines that use adhesives with a low environmental impact.
Assembly and finishing
In addition, Dreampell provides an organised area in the factory for the assembly and storage of components and the finished product. In this phase the product is assembled and finished using traditional and automated production systems that guarantee high quality and precision. Everything is managed by experienced workers who have developed skills over the years to perform this production phase, which requires craftsmanship and continuous training in the use of new machinery.

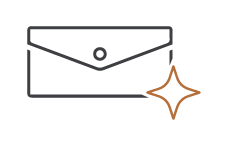
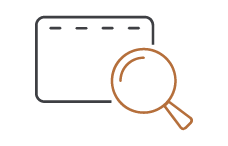

Quality control and packaging
Quality control takes place in Dreampell’s own facilities, where experts individually finish each product and inspect it several times before it is sent for packaging.
This part of the control process is essential to maintain high quality standards and to ensure that every part of the product meets the Made in Italy label.
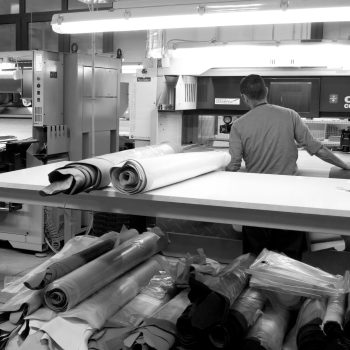

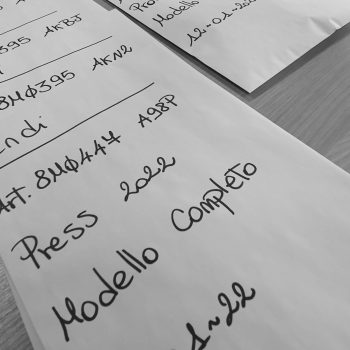


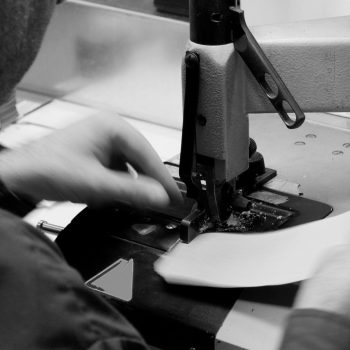
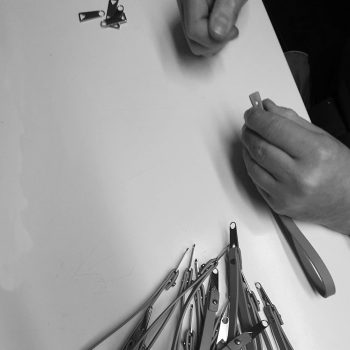


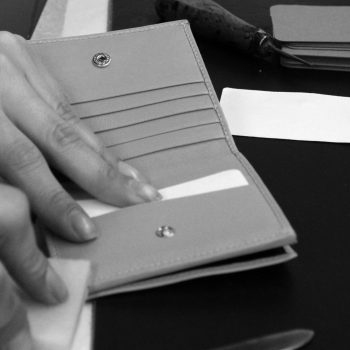

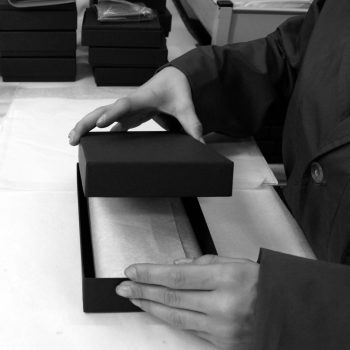
The Expertise
Dreampell’s expertise
The entire production process is carried out at Dreampell’s Scandicci-based facilities, where the company’s craftsmanship, expertise and high-performance machinery provide control over all phases of leather processing and the finished product.
Product development, modelling, cutting, preparation, assembly, re-finishing and testing for quality control of the final product with the customer: these are all the stages that the company is able to follow during the production cycle, including every aspect of processing.
The production process that the company has structured over the years is organised down to the smallest detail to allow perfect control over the individual stages of leather processing.
The services offered:
- Product development and pattern making
- Raw material quality control
- Die cutting or automatic cutting
- Preparation
- Assembly and finishing
- Quality control and packaging
- Shipping

Product development and pattern making
A dedicated pattern-making and product development area has been created within Dreampell’s facilities to provide specific support to customers so they can create, study, prototype and industrialise new products.
A team of dedicated experts develops creative designs through the use of technological processes and new programming tools that enable CAD finished models.
The company also offers the possibility of having models developed traditionally by hand.
From the customer’s sketches and style, Dreampell is able to develop the first prototype, which will be transformed into an actual model after various stages of defect clearance.
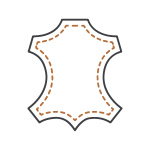
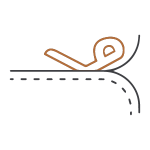
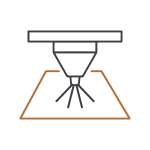
Raw material control, cutting and preparation
Logistically, Dreampell’s factory is designed to receive incoming materials, which are then checked before being sent to the various departments.
After careful inspection, the leather is transferred to the cutting department, which is carried out in-house or by detached companies working permanently for Dreampell.
The cutting is carried out using automatic machines and traditional dies, all of which are meticulously supervised by the head of the department.
After the cutting phase, the leather is sent to the preparation phase, where the raw material is brought to the desired thickness by splitting and fleshing.
Before arriving at the assembly stage, pre-assembly is carried out by means of robotic gluing machines that use adhesives with a low environmental impact.
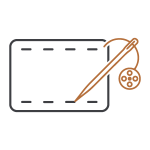

Assembly and finishing
In addition, Dreampell provides an organised area in the factory for the assembly and storage of components and the finished product. In this phase the product is assembled and finished using traditional and automated production systems that guarantee high quality and precision. Everything is managed by experienced workers who have developed skills over the years to perform this production phase, which requires craftsmanship and continuous training in the use of new machinery.
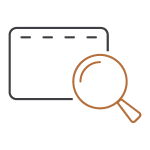

Quality control and packaging
Quality control takes place in Dreampell’s own facilities, where experts individually finish each product and inspect it several times before it is sent for packaging.
This part of the control process is essential to maintain high quality standards and to ensure that every part of the product meets the Made in Italy label.



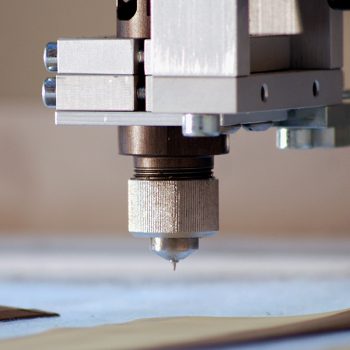

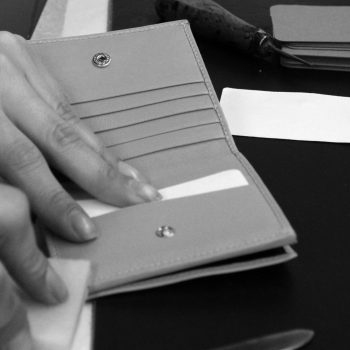
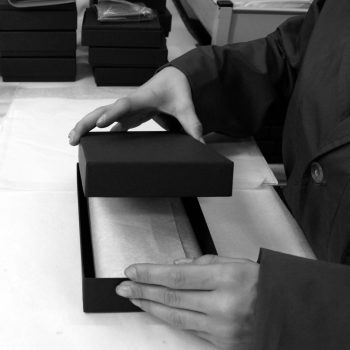
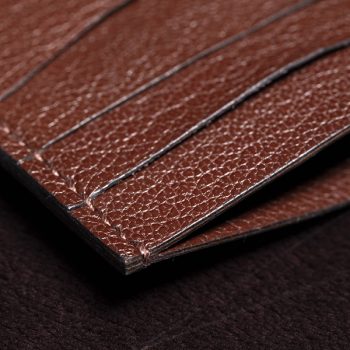
